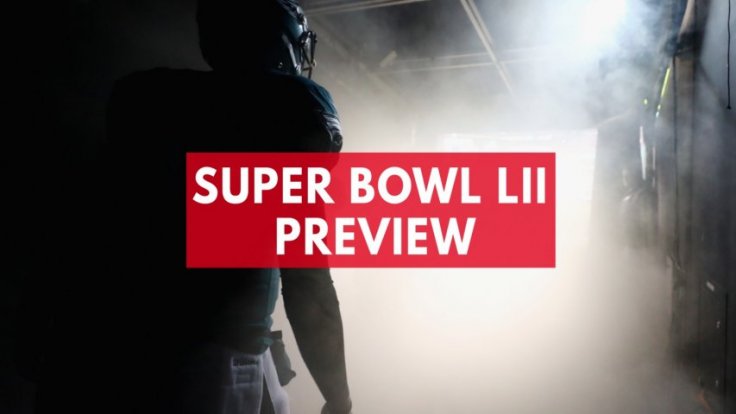
NASA has developed and tested its 3-D printed pogo accumulator, the new technological instrument used as a shock absorbing system in its RS-25 rocket engine. The beachball-sized hardware regulates liquid oxygen movement in the rocket engine which prevents vibration of the rocket.
NASA tested its newly developed technology in its RS-25 rocket engine which was launched on December 13. It could remove the pogo effect or the up-and-down vibrations in the rockets which are caused by its engines and propellants. These vibrations usually destabilize a rocket's flight.
NASA researchers claim that the new technology could reduce the production time of a rocket engine by 80 percent and reduce production cost by around 35 percent mainly through the elimination of the number of welds. Technicians could avoid around 100 welds which improves the flight experience by reducing vibrations.
Andy Hardin, the engine integration hardware manager for the SLS Program at NASA's Marshall Space Flight Center in Huntsville, Alabama, said, "As we build future RS-25s, NASA and our partners are taking advantage of innovative manufacturing techniques, including additive manufacturing, or 3-D printing, to make the engines more affordable. 3-D printing is revolutionizing manufacturing, and the pogo accumulator is the first of many components that can be built more quickly and less expensively."
The researchers say that innovation in the 3-D printing technology along with design changes could reduce more than 700 welds in more than 700 parts in the rock engine. This could significantly reduce the costs of production of rocket engines.
NASA and its industrial partner Aerojet Rocketdyne plan to use the technology in engine components like combustion chamber, nozzle, ducts, valves, electrical and running gears. It could improve the manufacturing process and increase performance, reliability, and safety. Engineers say that the 'next generation' RS-25 engine would have fewer parts and welds.
Carol Jacob, the RS-25 engine lead at Marshall said, "Reducing the number of welds is very important with each weld comes inspections and possible rework. By eliminating welds, we make the hardware more reliable and the process much more lean and efficient, which makes it more cost-effective."
The RS-25 would undergo three more tests incorporating new 3-D components during its certification procedures.
NASA has been doing series of research in the 3-D printing technology as a technology which could drive the near future. The invention of shape memory alloy (SMA), an engineered nickel-titanium alloy which would return to the desired shape after deformation, has become a major tool in the field.
NASA's Convergent Aeronautics Solution (CAS) Project aims to develop a feasible Spanwise Adaptive Wing (SAW) which would bend aircraft's wings in-flight to increase the performance and efficiency by reducing the weight and drag of the craft.
The aerospace agency has been working with Goodyear Company to develop special wheels which could adjust to the terrain by changing shape. This wheel has great significance in the future ground explorations in other planets and moons and can aid locomotion on Earth. These wheels would be resistant to wear and tear and hence could prove enduring for long-term use.
NASA believes that 3-D printed habitats would be effective for building shelters for explorers during their missions to Moon, Mars and other bodies beyond it. It has even organized a 3D-Printed Habitat Challenge in November 2017 for deriving ideas from the public for its future mission.
3-D printing also has wider application in the medical field, especially during surgeries, as it could be used in sensors and activators which supports organs as ultra stretchable bioprobes.