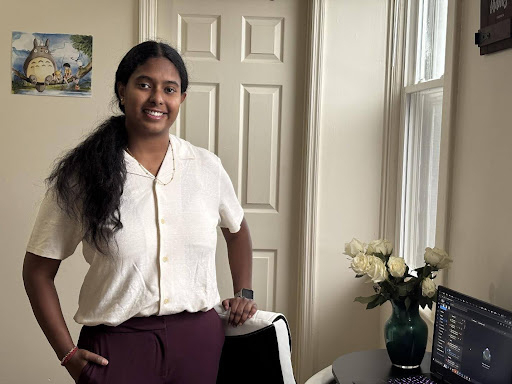
As the automotive industry evolves, the demand for greater efficiency, and sustainability in manufacturing processes has become essential. Internal Combustion Engine (ICE) vehicle manufacturing, while facing challenges from the rise of electric vehicles (EVs), continues to benefit from advanced engineering strategies that enhance productivity, reduce costs, and minimize environmental impact.
Engaging in the internal combustion engine development is Priyanka Das, an engineer who has worked rigorously on making the manufacturing systems smooth of automobiles.
At the Sharonville Plant, Priyanka manages two Powertrain Transmission projects and spearheads the manufacturing line launches for Ford F-150, Expedition, Navigator, and F-Series Super Duty trucks. In addition, she excels at resolving debugging control issues during commissioning and production. While at Tesla, she worked on battery pack assembly, cell manufacture, and inverter assembly for the Model 3, Model S, and Cybertruck.
She also helped OEMS align design specifications to Ford standards which is very important budget-wise and in maintaining standards. By improving the Controls implementation, she cut down downtime and launch time and ensured safety standards were being met for the processes.
Her leadership in upgrading manufacturing lines, delegating tasks across teams, and driving efficiency has solidified her position as an active influencer in ICE vehicle manufacturing.
Given her experience in ICE vehicle manufacturing, she lets us know about the key areas where engineering excellence can drive optimization.
Streamlined Production Processes
She tells us that to streamline the manufacturing process Robots and AI-driven systems can be employed for precision tasks, such as assembly, welding, and painting, reducing human error and enhancing quality. Further, creating virtual replicas of manufacturing processes allows engineers to identify bottlenecks, improve layouts before implementation and align production schedules with demand minimising inventory costs and waste.
Advanced Materials and Lightweighting
Material innovation plays a critical role in ICE vehicle manufacturing. High-strength alloys lead to reducing vehicle weight while maintaining structural integrity and improving fuel efficiency while composites and polymers are being increasingly used in non-critical structural components to lower overall weight and improve performance. Plus, in this scenario of environment consciousness recycling metals and using eco-friendly materials align manufacturing with sustainability goals.
Energy Efficiency and Sustainability
Speaking of global sustainability goals ICE manufacturing plants are adopting green practices to align with environmental regulations. They are increasingly adopting methods for real-time monitoring and optimization of energy usage within facilities. Plus, they are repurposing heat generated in production processes for other operational needs reducing energy consumption. Advanced water treatment and recycling systems are also being employed to reduce the environmental footprint.
Quality Control and Predictive Maintenance
Machine learning can be implemented via automated defect detection to improve accuracy in quality control. Further, sensors embedded in manufacturing equipment can detect anomalies, preventing costly downtime and extending machinery life leading to predictive maintenance.
Integration of Smart Manufacturing
The rise of Industry 4.0 has introduced connected systems to ICE manufacturing. Internet of Things (IoT) devices provide data insights for operational decision-making, big data analytics helps identify trends and areas for improvement, and cybersecurity leads to protecting interconnected systems safeguarding sensitive data.
Supply Chain Optimization
Efficient supply chain management is vital for the uninterrupted production of ICE vehicles. Transparent communication with suppliers improves material quality and delivery schedules. Further, blockchain technology can help track parts and materials across the supply chain which ensures authenticity and traceability. To reduce transportation costs and emissions she suggests sourcing components closer to manufacturing sites, which reduces transport costs and emissions.
Workforce Training and Development
Human resources remain at the heart of efficient production, Priyanka has implemented and advises providing training in areas like robotics, IoT, and data analysis as well as equipping workers with multiple skills to increase flexibility and reduce downtime. Plus, in the field of automated landscape, there is a need to ensure workers can operate alongside automated systems safely and efficiently.
Sustainable Manufacturing Practices
Adopting environmentally responsible practices enhances efficiency and reduces waste. This can be done by incorporating recycled materials into the production process. Implementing solutions like reusing and recycling water used in production and utilizing technologies to lower emissions from manufacturing activities can not only help organisations align with environmental goals but can also be a more efficient method for reducing waste.
Engineering excellence focuses on the harmonious blend of technology, efficiency and sustainability and the works of individuals like Priyanka Das can show how enterprises can leverage cutting-edge technologies to creatively tackle competition in the automobile industry while addressing the challenges of an evolving automobile industry.