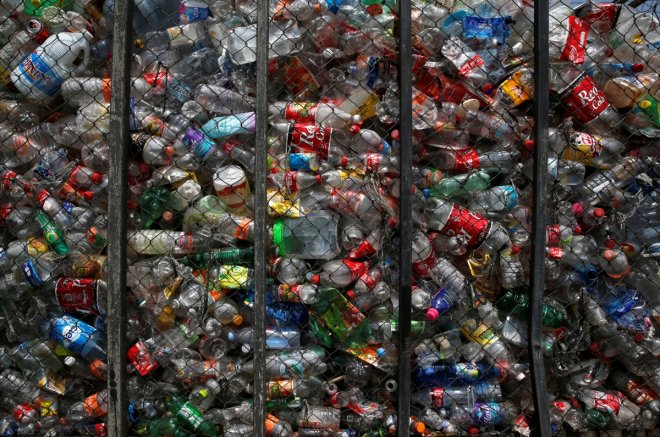
"China has found a new technique to create biodegradable plastics", researchers from the University of Nebraska-Lincoln, USA and Jiangnam University, confirms. The new bio plastic is prepared from renewable biomass sources, such as vegetable fats and oils, corn starch, or micro biota. Scientist stated that it can be derived from industrial plants such as Cargill plant in Blair, Nebraska, USA.
The process
Bio plastics derived from the new plant can help in improving the properties of plastics which in turn will assist in overcoming the obstacles of its commercial production. It is found that, by raising the temperature of bioplastic fibres to several 100 degrees Fahrenheit and allowing it to cool improves the bioplastics resistance to heat and moisture.
Time consumption and other expenses can be reduced through the thermal approach. This technique can also improve the commercial viability of bioplastics. Polylactic acid or polylactide derived by fermenting cornstarch, sugarcane and other plants is used as a major ingredient for this plastic. Polylactide can be used as an environmentally friendly alternative to plastic, which is made from petroleum.
Drawbacks
Susceptibility of polylactides to heat and moisture results in its limited use in textiles and other industries. L and D polylactide molecules were made earlier to create stronger molecules. The production of L and D molecules were costly and also they are difficult to pair with other molecules. The disposal of the solvents used also creates environmental issues.
Dr Yang, a professor of biological system engineering says "the problem is that people couldn't find a way to make it work and use it on large scale...People use nasty solvents or other additives which are not good for continuous production",
"We don't want to dissolve the polymers and then try to evaporate the solvents, and then consider revising them. That is just too expensive and unrealistic," he added.
The team rapidly heated the L and D polylactide at 400 degrees after mixing the pellets and spinning them into fibres. The resultant bioplastic resists melting at temperatures more than 100 degrees higher in comparison to previous L and D plastic molecules. It retains its structural integrity even after having submerged in water at more than 250 degrees. These properties can be used in the textile industries.
The new plastic which is being prepared at the Yang's lab will make its commercial advantage when incorporated in the existing industrial process.